Research
We, at FRACH robotics, are fascinated with a prospect of having inexpensive humanoid robots at our homes. However to achieve this goal we need to first develop animalistic type of robot locomotion and also inexpensive and human safe robot muscles. As we are closely following the latest university research in these areas we believe we can develop our first soft-robot product (Gripper) in next 2 years.
Utrecht University and University of British Columbia research of muscle based control with neural delay to simulate bio-mechanical constraints.
Google DeepMind AI research of walking bi-pods using self-learning deep neural networks.
Cornell University research of soft robotic muscles.
Harvard University research of small soft robots.




Small Scale Production
Small scale production of electronic gadgets has been always a concern for its high investment and operational costs. For example, the high-quality steel plastic injection molds for a small robot can easily cost upto £100000.
Therefore we, at FRACH robotics, have developed the SASS (Smart Agile Small Scale) method to minimize the costs, focus on fast delivery of the business value to our customers and risk mitigation at it's core. Our SASS method covers comprehensively all aspects of design, manufacturing, testing and fulfillment and it is strongly inspired by the IT industry best practices such as Agile, DevOps and Micro-services.
-
3D design - using inexpensive 3D CAD SW, such as FreeCAD or AUTODESK Fusion 360.
-
Off-the-shelf HW design - component design based on reusing currently manufactured and easily sourced modules such as Android devices, geared motors, common DIY electronic modules, rubber transmission belts, etc. Focus on sourcing from multiple channels to minimize dependency risks and costs.
-
Off-the-shelf SW design - robot SW functionality and its behavior is tightly integrated with Android available public APIs and services. Such as Google Android speech recognition API, Google Android TextToSpeach API, Google Assistant, Google Youtube, Google Drive, Google Mail and Microsoft Skype. This design approach significantly extends robot's capabilities, but reduces the costs.
-
Rapid prototyping - using FDM 3D printers with 0.8mm nozzles for fast and 0.4 nozzles for more precise plastic parts prototyping; with PLA plastic for low environmental impact and recyclability.
-
Rapid mold patterns - using SLA/DLP 3D printers with UV resins to achieve high quality mold patterns with 50 microns resolution.
-
Rubber plastic injection molds - using RTV silicone and thermoplastic PVC rubbers for inexpensive and recyclable injection molds; reinforced with fiberglass threads.
-
Aluminium plastic injection molds - using inexpensive aluminium mold production technique based on the sequence: SLA 3D printed mold pattern / rubber mold / refractory plaster mold / vacuum assisted melted aluminium mold; where the aluminium molds can be also used directly in the plastic injection molding machines. Also with the benefit of aluminium recycling.
-
Polyurethane plastics - low viscosity vacuum assisted injection molding without expensive injection molding machines for low production volumes. Adding chopped glass fibers for extra strength, durability and crack resistance.
-
Outsourced plastic injection molding - renting local available capacity and using low cost aluminium molds for standard plastic injection molding for medium production volumes.
-
Outsourced electronic PCB manufacturing and assembly - using online outsourced services, where a PCB is manufactured, assembled and delivered in 4 weeks. See bellow an example from our main PCB manufacturing partner; Seeed Studio.
-
Self-assembling design - designing both plastic and electronic PCB parts to simplify, mechanically guide and speed up the assembly of the final product with focus on mitigation of wrong direction/parts assembly.
-
Batch assembly - using mass production techniques introduced by H. Ford to break down complex assembly processes to tens of simple assembly steps, which can be executed in batches of 100s.
-
ISO quality - quality method focused on reproducibility, where the assembler is provided with visual and video description of each simple assembly step and with all required assembly tooling. So, the assembly batch is executed in the continuously same quality and productivity.
-
SW Agile, DevOps and Micro-services - using the IT industry SW development best practices to continuously analyse, develop, test, deploy and assess business feedback in short monthly cycles. Breaking down complex SW packages to small components with defined interfaces to simplify, parallelize and de-risk the SW development. Totally automating repeatable processes, such as build, test and deploy.
-
Agile delivery of the business value - iteratively deliver the latest functionality and bugfixes to the customer base every few months over the Internet.
-
Outsourced fulfillment - outsourcing fulfillment of the end product to global efficient professionals to minimize costs and environmental impact. Prefer local over global.
-
Customer feedback - support multi-channel customer feedback on social media and forums to truly understand customer wishes, desires and new trends. Involving the customer base in selection of new functionality, capabilities and products. Running small focus groups for simple and inexpensive product marketing research and product capabilities assessment.
-
Research & development - staying on the top of the latest University research and following the latest open sourced technologies from major SW companies.

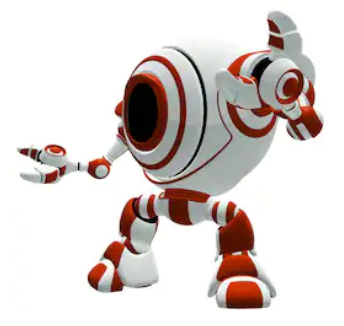


Prototyping
Agile delivery methods require a short iteration life-cycle of analyses, design, test, user feedback and improvement. It is necessary to innovate, test and accept/reject all parts of the design in fast and fine granular matter to maximize business value, mitigate delivery, quality and user acceptance risks and minimize the development, production and product costs. On the picture below you can see history of our prototyping cycle for last 2 years.
